STD Rocket launch
In 1962 Neil Brown returned to the United States to join a company called Hytech in San Diego, California, to continue the development work started at WHOI. Hytech was formed in 1960 by Don Cretzler and initially, it made bathythermographs, current meters, and a wave and tide monitor. These were amongst the first electronic ocean instruments. Neil Brown joined the company to develop a laboratory salinometer (see Development of Salinometers).

Soon after, he designed the electronic components that were
the key to making in-situ measurements of salinity enabling the first STD to be built in 1964. The following year the Navy contracted with Hytech and Santa Monica, CA, based Bissett-Berman, who was one of the few companies at the time with computer technology. Together they made the first automated ocean data collection system that was used to collect large volumes of data. As a result of this collaboration, Bissett-Berman acquired Hytech. In 1964, the Navy awarded them a contract to develop the first oceanographic sensors capable of continuous operation for up to one year in-situ. This was followed by other Navy contracts for specialized sensor systems. In 1969, the San Diego division moved into a 33,000 square foot purpose-built building in Kearny Mesa, CA. In 1970, Bissett-Berman was purchased by the British company Plessey Ltd. and the San Diego Division was renamed Plessey Environmental Systems.
This instrument measured Conductivity, Temperature, Pressure (CTP), but because the instrument implemented the “salinity and depth equations” in complex adjustments of internal analog electronics, and these values of Salinity, Temperature, and Depth were transmitted to the surface, the instrument became known as ” STD”, or “S/T/D”.
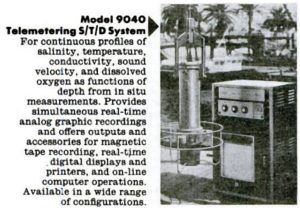
The Plessey S/T/D systems were on the market from 1964 to 1980, with popular Telemetering S/T/D 9040 and Self-recording S/T/D 9060.

At that time, computers and their peripherals were expensive, not very reliable, and difficult to use at sea. Since it was essential that salinity measurements were available immediately, the complex relationships between salinity, temperature, pressure, and conductivity had to be simulated using a “salinity bridge”. This bridge consisted of two platinum temperature sensors and three thermistors, two pressure sensors and six transformers, as well as an inductive conductivity cell and important electronic circuits. Its calibration required numerous and complex settings and adjustments.

The STD’s accuracy was not adequate for depths much greater than 1,000 meters, and there was a severe “spiking” in the salinity data, due to the slow response of the temperature sensor relative to the conductivity sensors. Also, its accuracy was limited by systematic errors in the salinity bridge emulation of the salinity, pressure, temperature, and conductivity relationships.
Two aspects of the inductive conductivity sensor have limited its commercial applications to the measurement of Oceanographic salinity and density. First, the large thermal mass of the sensor relative to the volume of water that passed through it from the inside, which led to a thermal error in the measured conductivity.

The electrical conductivity of a liquid depends strongly on the temperature at which it is measured. If, due to the presence of the thermal mass of the sensor, the conductivity sensor heats or cools the volume of water it is trying to measure, this will lead to inaccuracies in the calculated salinity/density.

Since Oceanographic sensors are often used at significant depths where the surrounding water pressure can reach 700 bar, the magnetic cores of the sensors were installed in a pressure-proof metal housing. Then the pressure protection housing had to be covered with a dielectric material to prevent the metal housing from short-circuiting around the sensor.
Second, the large non-contact external field can be affected by other structures associated with the CTD device, such as auxiliary sensors, protective frames, etc. These external structures change the free current flowing through seawater. Consequently, their effect cannot be distinguished from changes in the conductivity of seawater, and they introduce a mixing variable.
“The routine use of continuous profiling instruments such as the STD introduced a decade ago showed very clearly that the ocean structure was very much more complex than the classical Nansen bottle data would suggest.” N.Brown, 1974